True determination: Pradosh Kumar Rath
With the goal firmly in sight, Pradosh kumar Rath, Chairman-cum-Managing Director of Rashtriya Ispat Nigam LimIted, knows the company has the infrastructure and passion to get there.
With more than three decades of steelmaking experience, Pradosh Kumar Rath, Chairman-cum-Managing Director of steelmaking giant Rashtriya Ispat Nigam Limited (RINL), brings a wealth of industry-wide experience and expertise to the company.
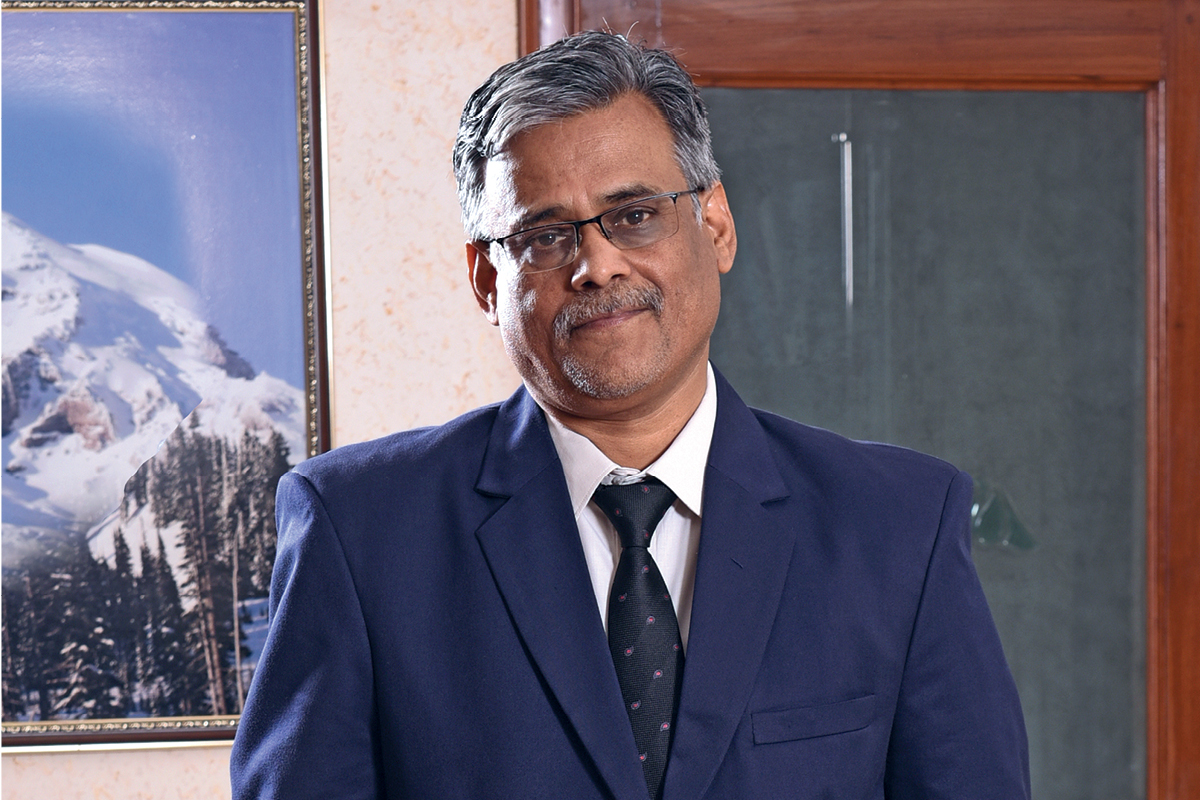
Founded in 1982, RINL is a holding company consisting of two plants. One of them is Visakhapatnam Steel Plant, better known as Vizag Steel – India’s first shore-based steel plant and among the lowest cost steel producers in the world, specialising in value-added steels, special steel and steel wire rods.
The other is RINL’s forged wheel plant in Rai Bareilly, which from September 2019 will manufacture and supply forged wheels to the Indian Railways.
Achieving ‘Navratna’ status in 2010, RINL has additional advantages and greater autonomy to compete in the global market than other public service undertakings (PSU) in India. There have been only 16 companies awarded this status in India.
Since stepping into the Chairman-cum-Managing Director role in 2018, Rath has overseen a significant capacity expansion and infrastructure diversification. "When I took over the plant, we had increased our capacity and were on the verge of making 4.5 million tonnes of liquid steel," Rath recalls. "My first goal was to ramp up production to achieve full capacity utilisation and production of 7.3 million tonnes of liquid steel."
As a result, Rath has seen a turnaround in the company. "The plant was originally established as a three-million-tonne plant but was almost written off as it wasn’t considered viable," he remembers.
"Someone who comes from within an organisation can identify areas to concentrate on."
"The dedication of the workforce has turned RINL around, and no doubt changed the fortune of the company. We’ve got a very committed team. The plant had incurred losses over the past three years, and my goal has been to bring the company back and make it profitable and sustainable."
Having been with the company for over 36 years, Rath has an invaluable knowledge that comes from understanding the different roles and components of the business. "I joined as a trainee so have observed the shortcomings of the plant in different areas of administration," Rath reflects.
Coming from within the organisation, Rath is well aware of the areas to concentrate on, which also gives him strength to steer this company to greater heights. "During my tenure with RINL, I’ve seen a transformation in our staff and culture," he adds.
"We now have a very committed workforce, who will change the direction of the company. Their commitment, along with the quality of our raw materials and infrastructure, gives me hope that we will achieve our targets."
But increasing production on this scale doesn’t come without challenges, so the company is ensuring its infrastructure can manage this increased volume through astute planning and preparation. "The main dynamic we need to factor in is logistics," Rath says.
"When we ramp up production to our required capacity, the volume of operation also increases. This means we need to optimally manage the logistical movement of inward raw material and outward finished steel.
"We’ve commissioned one central dispatch yard to make the dispatch process more efficient. We’ve also upgraded our equipment so we can efficiently manage the inward volume needed to sustain this increased level of production."
Upskilling RINL employees is a priority for Rath so the staff can support the growth in infrastructure and production goals. "As a company, we have only one focus and that is achieving our goal of 7.3 million tonnes of liquid steel production," he states. "We are doing everything with our infrastructure, processes and people to achieve this."
Steel production is very energy intensive and the energy source used constitutes a significant cost of the steel operation. About 70% of energy consumed in total steel production is from coal and coke inputs.
In fact, an estimated 1.2 billion tonnes of coal are used globally for steel production, accounting for 15% of the total coal consumption worldwide.
"Two factors will determine the fate of the company – achieving production goals and decreasing coal consumption."
RINL currently utilises coal as its primary energy source; however, in a bid to conserve energy and minimise its environmental impact, the company has been exploring alternatives to bring coal consumption down by implementing pulverised coal injection in the blast furnace.
"Two factors will determine the fate of the company – achieving production goals and decreasing coal consumption," Rath predicts.
Customer relationships and strategic supplier partnerships have been crucial to the success of the business. "We have two types of customers – those who supply material to us and those we supply the finished products to," Rath says.
"Both types of customers have been with us since the plant was commissioned in 1990. That’s 29 years of committed and mutually beneficial relationships.
"To be successful in any industry, you need to keep the customer in view and we keep both firmly in ours."
Proudly supported by: