Why is operational management so afraid of variance?
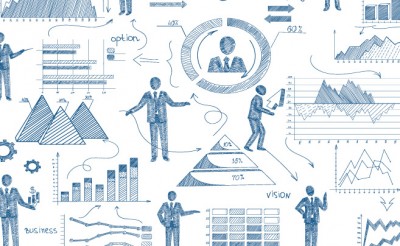
In my work with organisations of all shapes and sizes, variance to plan is one of the more painful and difficult aspects of operational management to deal with. The reason for this is fairly straightforward. Variance goes against the hitting plan and delivering what you say you will deliver is a key management skill upon which all successful businesses rely.
The tried-and-true strategy to prevent such pain is to build in contingency. We make allowances for what could go wrong and build them into planning, thus significantly increasing the likelihood of success.
What this operational management technique reveals is a large opportunity to outperform stated targets. What if we manage to stop the problems occurring? We will outperform the forecast and return more to our shareholders and owners and be more competitive in our market.
Plan twice
The best-managed companies therefore have two sets of operational plans. There is the plan publicly committed to, with all its contingencies and allowances built in, and there are the internal operational plans that have no contingency built in.
These internal plans can only be achieved if nothing at all goes wrong. The power of this is that if the organisation fails to achieve it, you have a tangible measurement that something went wrong, creating the opportunity to improve. The Lean management method of plan, do, check, act, is quite impotent if there is no action required because plan is always hit. In such a case, the plan is most likely too easy. Stretch targets should be just that—only achieved at a stretch.
It is this lack of contingency in an internal operational plan that makes it difficult to implement. Most middle managers have more than one boss. First, there is the boss on the organisation chart who must be kept satisfied at all times and then there is the second boss—the manager’s own career ambition—and when the two come into conflict, the manager’s own career ambition wins every time. When it comes to missing a target or plan, the energy and effort therefore goes into satisfying the manager’s own career ambitions and therefore the outcome is likely to be, it wasn’t my fault.
KPIs vs career
Being comfortable with variance, being willing to confront a missed plan takes a remarkable and uncommon management skill, which is the maturity to differentiate between the KPI itself and one’s own career aspirations. It is actually a high management skill to be willing to commit to a plan that requires a lot of things not in one’s control to go well in order to be met, and then when things do indeed go wrong, to identify the root cause and play a key part in fixing the underlying problem to prevent the problem occurring again.
3 tips to set up an internal plan that delivers operational improvement
- The plan should have no or a very limited contingency. This drives high performance and focuses managers on what they need to do to succeed.
- It should occur in a no blame If the plan requires nothing to go wrong in order to be met, by definition it is not the manager’s fault when something goes wrong. Instead, the manager is dealing with a systemic or process failure.
- It should occur where a clear-headed review of what happened is undertaken with a view to prevention.
We see this operational management technique in the huge improvement of OH&S in industry over the past few decades where the focus is unrelentingly on prevention.
Variance to plan is an uncomfortable place to be but that’s how businesses improve their operational performance. If you don’t have any, you are going backwards.